Antig's core technology is it's innovative H2PowerChip™
design which is built around printed circuit board (PCB) technology. This design
allows for the creation of a micro fuel cell that has a high power
density (output) to size ratio. By leveraging
existing IT manufacturing materials and techniques Antig has
also been able to reduce fuel cell cost barriers while ensuring
improved system performance and
reliability. All critical elements required to support
the widespread adoption of fuel cell technologies.
The Antig
H2PowerChip™ is the core
component that goes into a fuel cell. As the main building block of a stack, it's
size and weight determine overall performance. Each cell
on an H2PowerChip™ is responsible for generating the power
required to run a device or charge a battery. These
cells are packed together with a single step hot press
lamination process. (To learn more about the reaction
that occurs inside a cell, please view
How Fuel Cells Work.)

An example of Antig's 4 watt
H2PowerChip™ module |
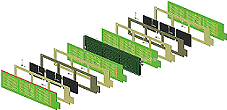
Antig's lamination process
|
After H2PowerChips™
have been
created, they are layered
together (stacked) to generate a specific amount of power. The
size and number of chip modules that go into a stack are ultimately
determined by the type of device that the stack is designed for.
For example, higher power fuel cell systems require larger stacks to
support the power demand. However, with a larger stack comes the
need for greater power management as well as additional thermal
and fluid control. This adds to the overall complexity and
size of the system. Conversely, a low power fuel cell system
can be quite compact, as it needs a smaller stack and has less
management requirements.
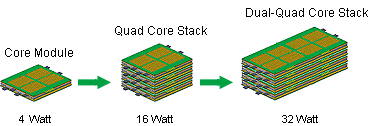
An example of increasing power by adding
H2PowerChip™
modules to a stack
|